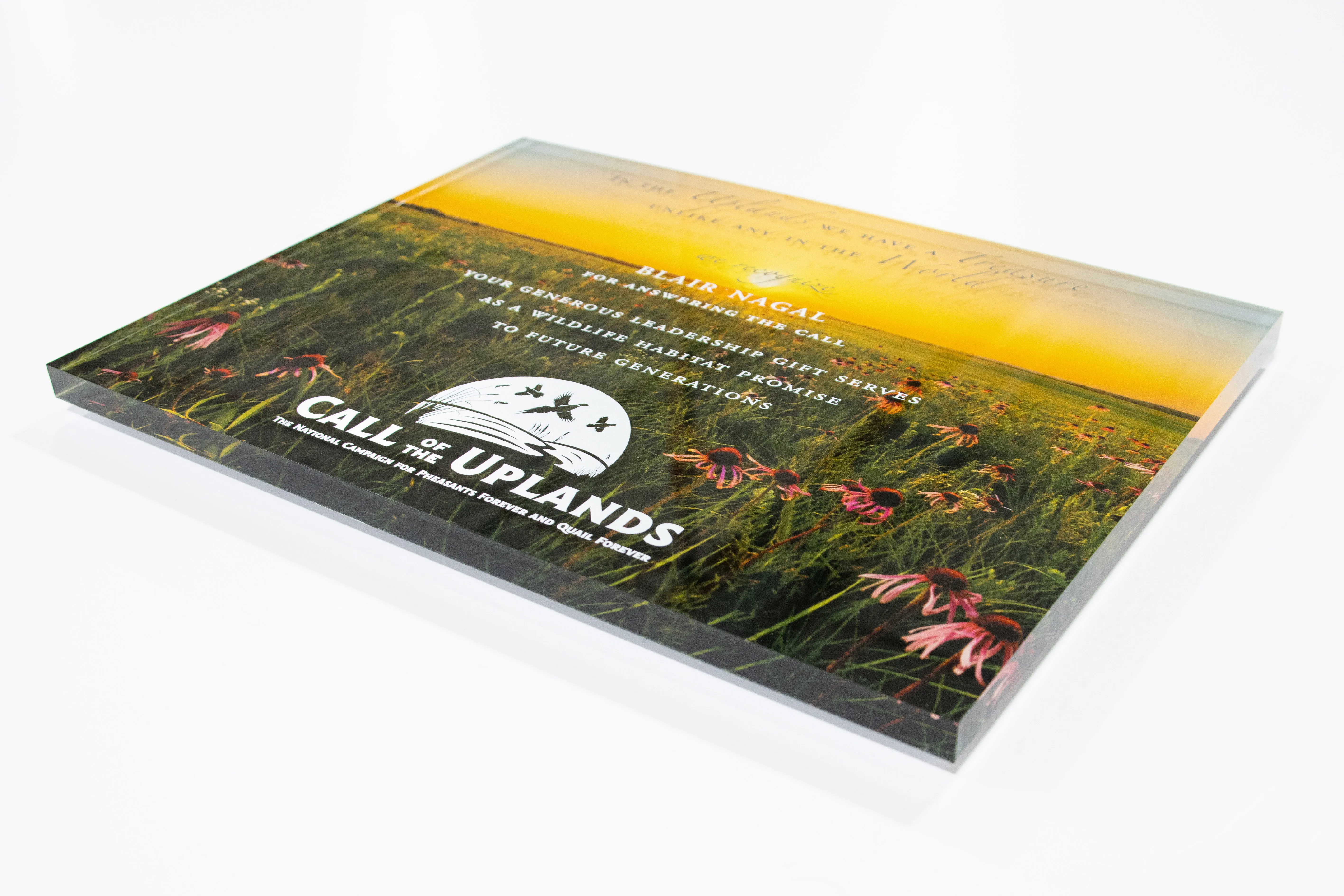
Would First, Second, or Dual Surface Printing Be Better for Your Project?
If your project involves printing on a transparent material – e.g., plexiglass, polycarbonate, client-supplied glass, mylar, polyester films, or vinyl – there are several visual effects and benefits you can achieve based on which surface the ink is printed on and viewed from. Transparent material has a thickness. This thickness introduces a third dimension to consider. You and your Infinity Images representative will need to determine the best printing surface process to achieve the effect(s) you desire. Read on to learn the difference between first, second, and dual surface printing, and the various benefits, applications, and considerations for each.
UNDERSTANDING THE DIFFERENCE BETWEEN FIRST, SECOND, AND DUAL SURFACE PRINTING
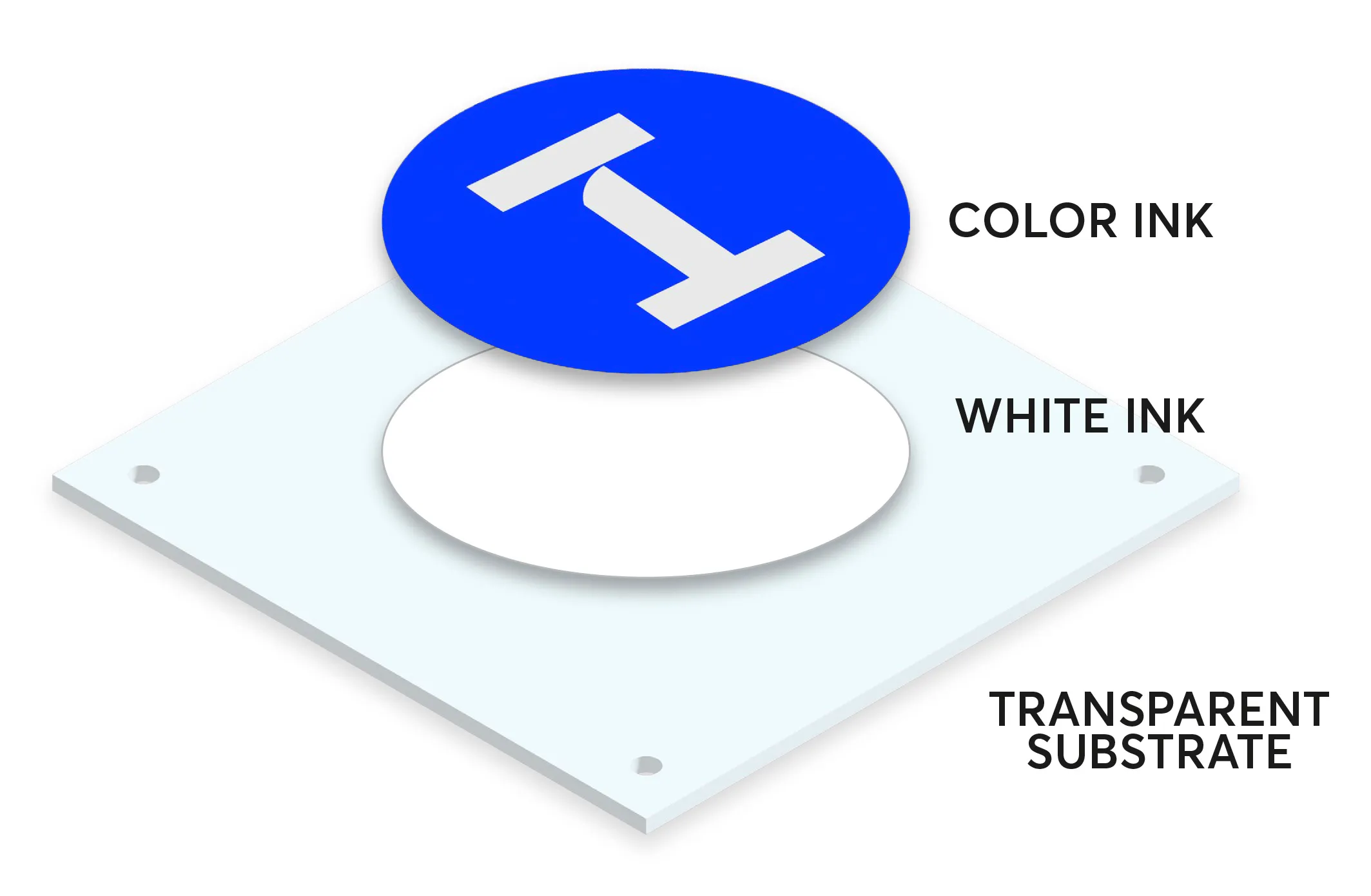
First Surface Printing
First surface printing involves printing directly on the front side of the material so that the ink is closest to the viewer. When light shines on the printed image, it will cast a shadow around the image and below through the thickness of the material, giving your image the appearance of depth. This shadow will not be visible if the material is a thin vinyl. However, if your material is a ½” piece of plexiglass, the shadow will be a noticeable element in your final graphic. This is the most standard printing method and is used for printing on all materials that are not transparent.
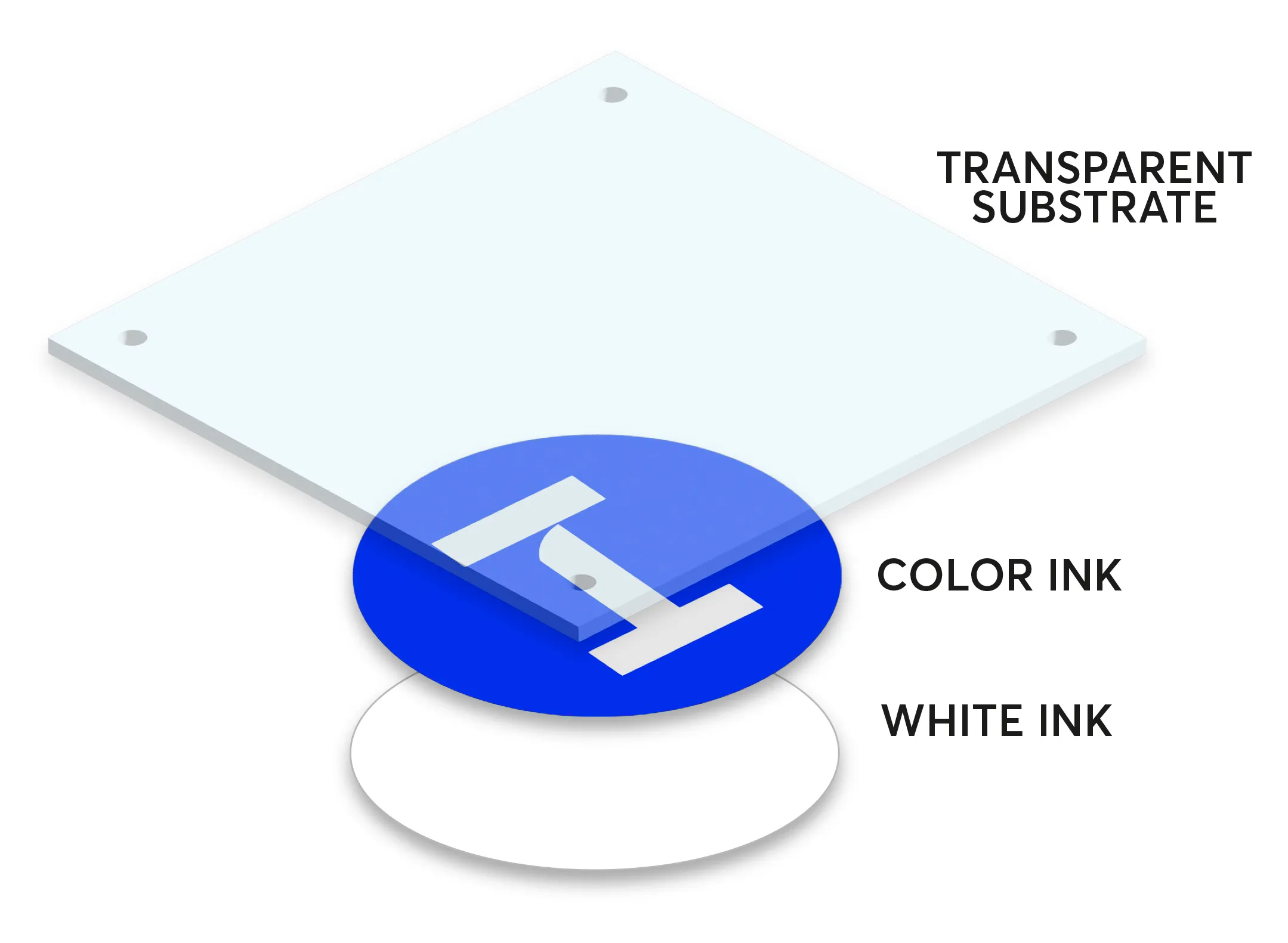
Second Surface Printing
Second surface printing involves printing on the back side of the material, with the purpose of the image being seen through the transparent substrate. This means the substrate will affect how the image below ultimately looks, such as adding additional shine or color tints, to name a few.
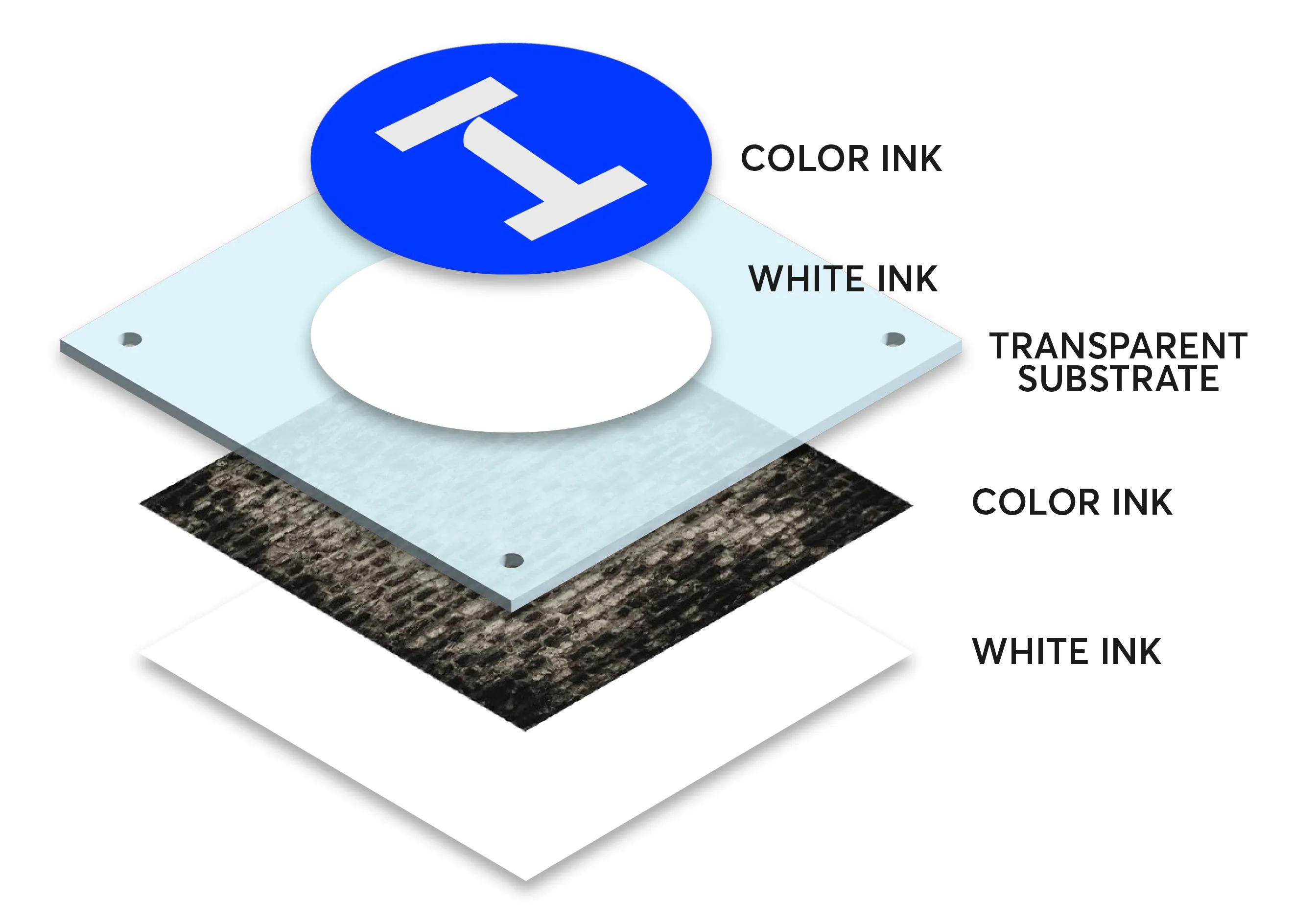
Dual Surface Printing
Dual surface printing involves printing on both sides, front (first surface) and back (second surface), of the material. This layering utilizes the dimension between the printed surfaces equal to the thickness of the material, giving depth to the piece.
Here is an example to better illustrate the process. Let’s say you print a picture of a person on the second surface of a piece of clear plexiglass. Then, on the first surface, you print a text box with the person’s name. The text box and name would appear to float in front of the person’s image, casting a shadow on the image below. If the piece is viewable from the back side, the text will not be visible behind the image of the person due to the layering. These potential obstacles will need to be considered if your piece is viewable from both sides.
BENEFITS AND APPLICATIONS
First surface printing is universally applicable to all materials. Any transparent or translucent material that our large-format printers can print on – plexiglass, polycarbonate, client-supplied glass, mylar, polyester films, or vinyl – can be printed first surface. Graphics printed on the front surface are often the most readable and can feature specialty printing methods like raised ink for dimensional effects and spot varnish for varied texture applications.
Second surface printing is generally considered a more premium method. This printing method greatly reduces the likelihood that the ink will be scratched off, an important consideration if your project will be featured in high-touch areas. It also reliably retains the gloss or matte of the original material, adding dimensionality to an otherwise flat graphic, and takes edge-lit graphics to the next level. Applications include wall standoffs (logos, text, photos, museum info panels), window graphics, certain room or brand signage, art displays, edge-lit graphics, and multi-layered displays. There is typically not a price difference between first and second surface graphics on the same substrate.
Finally, dual surface printing is a fantastic choice for projects that will be viewed from both sides, or that will only be viewed from the front but benefit from depth and shadowing. We’ve found that, when seeking depth, the thicker the material, the more significant the impact. This more premium process of dual layering has a few things to remember. Printing two layers requires twice the passes through the press and, therefore, is more expensive. Thicker material is also more expensive and has other considerations like weight, transparency, and overall effect on the image. Perfect applications for this premium process include award plaques, certain room or brand signage, art pieces, wall standoffs (logos, text, photos, museum info panels), and multi-layered displays.
WORKING WITH US
As is frequently the case, we recommend you start by having an in-depth conversation with your Infinity Images account representative. In this initial discussion, we’ll ask for details such as the impact you’re hoping to achieve, any concerns you may have about the environment your graphic will live in (e.g., front vs backlighting, touch zone, overall size, weather or temperature control, anchoring attachment availability, etc.), the desired longevity and durability, and finally, budget. Once we understand the full scope of your project, we’ll help you determine the printing method – and any additional specialty finishing methods, tints, opacity, white ink, routing, etc. – that will be the best solution to achieve your graphic goals. If you don’t yet have an existing Infinity Images account representative, contact us to get started. We can’t wait to work with you!